Solvent Extraction Plant :
Our Solvent extraction plants are used to extract oil from Rice Bran and All types oil cakes (sunflower, jatropha, groundnut, Soya Bean cake/flakes etc.)
Solvent Extraction Process
The process consists of extracting most of the oil from prepared raw material by Counter Current Extraction for a calculated period of time. Extracted meal from extractor is transferred for recovery of entrapped solvent to desolventizer toaster, where solvent from the meal is removed as well as the desolventized material is conditioned by controlling and adjusting the temperature and moisture. The conditioned desolventized toasted meal is sent for bagging. Vapors from desolventizer toaster are carried to condenser for vapour / solvent condensation & recovery of solvent via Economizer. Solvent after removal of moisture is re-circulated. Miscella after fine separation is pumped / feed to distillation section comprising of Evaporator, Heater and vapor condensing unit. Miscella is transferred to Evaporator via economizer where miscella is initially heated up and part of solvent is recovered by utilizing heat vapors from desolventising unit.
Maximum solvent from oil – solvent mixture is recovered at distillation stage. Final solvent traces from oil coming out from distillation zone are recovered in oil stripper working under vacuum.
In this plant, all extraction operations are carried out in closed equipment working under vacuum to avoid any solvent loss by evaporation. Air entrapping with the system along with solvent is passed through recuperation system where solvent traces from outgoing vent gases / vapors are recovered by absorbing the solvent in absorbing liquid. Hexane from solvent absorbent is recovered by heating the mixture and condensing solvent. This solvent free absorbent oil is again used for recuperation / recirculation.
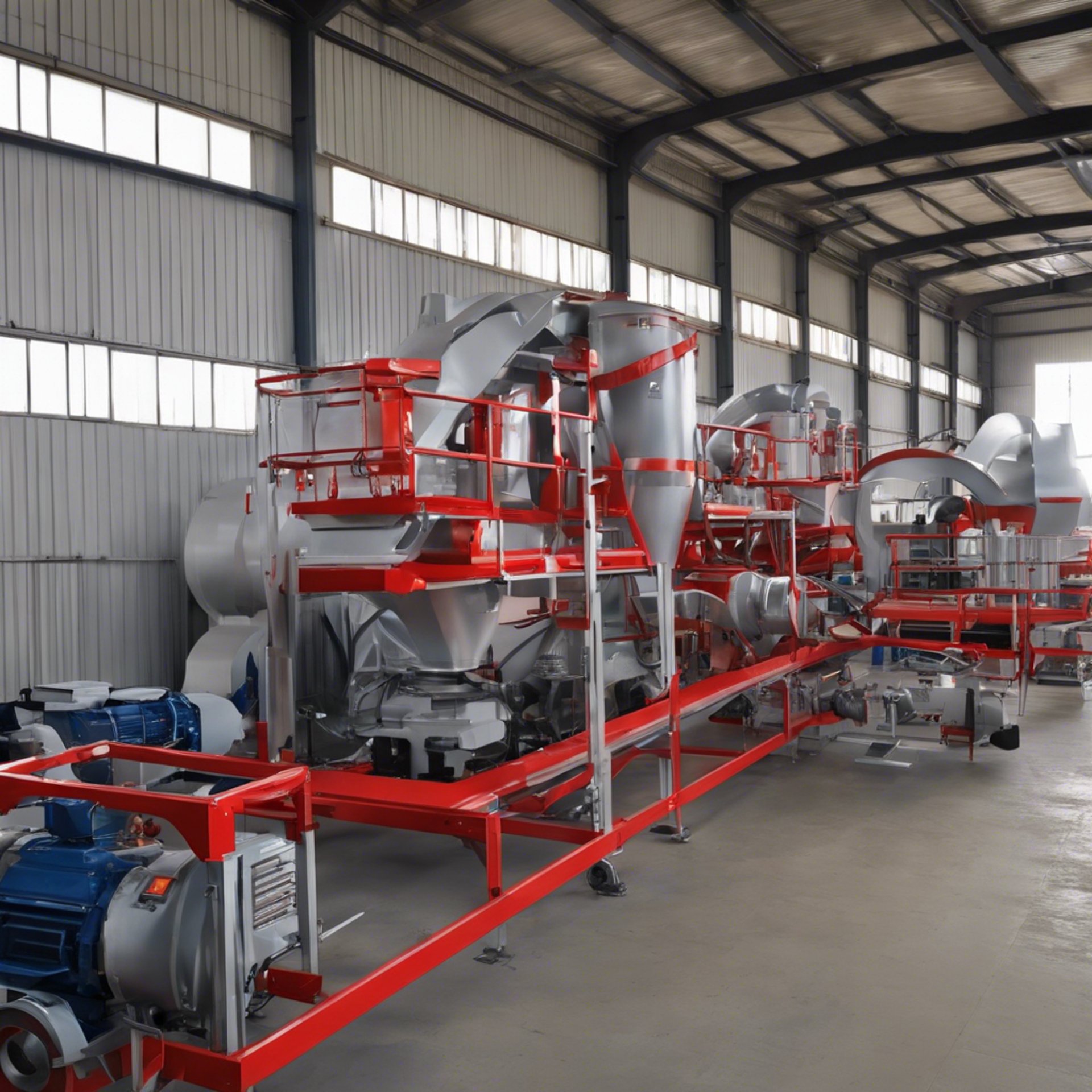
Details of Feed Plants:
At BIPL most advanced technology and innovative solutions are implemented to create state-of-the-art feed making machinery that are used around the world. Our machines are specifically designed for applications that require high capacities, power efficiency and uniform particle size. This provides our customers with confidence in knowing that we have the ideal machine for their unique requirements.
Our machines are based on proven technology and ensures to give high quality end product. Our machines are also known for their high productivity. The machines are designed and manufactured under stringent quality measures and extensive testing ensuring production of best quality feeds.
BIPL manufactures quality oil expeller machines ensuring that while expelling the oil :
Maximum oil recovery is done with minimum power consumption
The cake is not burnt
Proteins, vitamins and nutrients are not damaged
Colour fixation of oil does not take place
Minimum heat is generated while expelling process
Moisture does not find its way with extracted oils
Filtration is done in such a manner that no cake particles remain in contact with oil, thus FFA of oil is not increased.
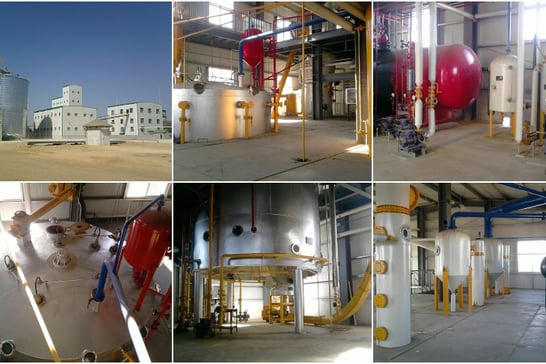
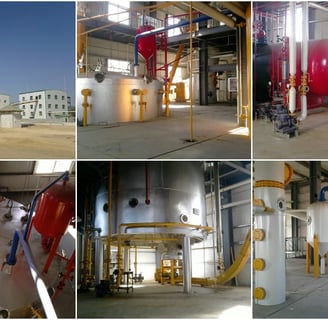
Details of Oil Expellers:
First Method:
Only pre-pressing is done in which case seeds are lightly pressed and leaves about 14% to 18% oil in the pressed cake. This method results in higher capacity; lower power consumption, lower wear & tear / maintenance. It is recommended when the buyer has his own solvent extraction line, so that balance oil is recovered during solvent extraction process.
Second Method:
When pressed cake is to be sold in the market, it is desirable to recover the maximum oil by Mechanical Extraction. Hence double or more pressing system is recommended. Here either in the same screw press - two stage pressing is carried out or pre-pressed cake from first stage screw press in sent for second pressing to other screw press. The oil left over after double pressing varies from 5% to 9% depending on the oil seed and extent of pressing.
Special Preparatory Required Equipments:
Any oil-bearing seeds can be processed in an oil mill (mechanical extraction system), special preparatory equipment are recommended prior to expelling. For Cottonseed, Sunflower seed, Groundnut seed- Decorticators are recommended. For Copra and Palm kernel- Cutters & Hammer Mills are required as preparatory equipment.
Special Preparatory Required Equipments:
Any oil-bearing seeds can be processed in an oil mill (mechanical extraction system), special preparatory equipment are recommended prior to expelling. For Cottonseed, Sunflower seed, Groundnut seed- Decorticators are recommended. For Copra and Palm kernel- Cutters & Hammer Mills are required as preparatory equipment.
Details of Edible Oil Refineries:
BIPL’s new generation Physical Refinery Plants are ideal solution for minimizing processing cost & processing loss. For high FFA oils such as Palm Oil & Rice Bran Oil this process is most common
Physical Deodorizing Section:
Deodorizing is nothing but The DISTILLATION process. in which fatty acid is distilled from oil. Under high temperature condition and in presence of high vacuum, with the help of sparging & agitation steam. Further this fatty acid in vapors form, is condensed & recovered in liquid form by the vapors scrubbing system. De-waxed / Bleached oil from intermediate storage tank is pumped by to primary heating plate heat exchanger which is used only in startup conditions. To heat the incoming cold de-waxed oil. Further it will be travel from oil to oil heat exchanger. Where de-waxed oil is getting heated by the outgoing hot refined oil. Then this oil is goes to The PRE-HEATOR via Peripheral coils of the regenerative heat exchanger which is the bottom compartment of the multipurpose deodorizer. In regenerative heat exchanger de-waxed oil flows through the coils & refined oil flows through the open space of the exchanger. In counter current manner, continuous steam agitation at open steam side assures continuous and maximum heat exchange. After recovering maximum heat from the refined oil. Oil is further heated up to the required temperature , suitable for the deodorizing in final heater. This heater is equipped with agitation and sparging steam, continuous flow of superheated steam through this assures effective primary vaporization of fatty acid.
Vapour Scrubbing:
The volatile matters consisting of free fatty acid and other odoriferous substances stripped from the deodorizer are led to the vapor scrubber located at the outside of the deodorizing column. In the scrubber volatile material rises through the bed of pall rings and meets liquid fatty acid sprayed from the top. vapors are condensed, cooled, and then recalculated to condensed fresh vapors. Excess distillate collected is led to the storage tank, whenever high level reached in storage space below the scrubber. Fatty acid scrubber is specially designed for minimum carryover of fatty materials, to the vacuum system.